Millable Materials for the Modern Laboratory
Alan Jurim, DDS | Barbara Jurim, DDS
Ask any dental technician, and they are likely to tell you that most client prescriptions direct the laboratory to decide what materials to use when fabricating the desired restorations. This approach, however, is far from ideal for a number of significant reasons. First, because the prescribing dentist best knows the patient’s dental history, relying on the technician to determine which materials are best can be problematic. Second, the desired restorative materials should be selected prior to tooth preparation because they will dictate critical clinical parameters (eg, margin design, occlusal clearance, facial reduction, etc). Third, a clear understanding of material indications allows the dentist to prescribe applications with the most predictable, long-lasting outcomes. To help the restorative team in determining the best treatment plan for each patient, this article provides a review and update of the millable materials currently being used in dentistry.
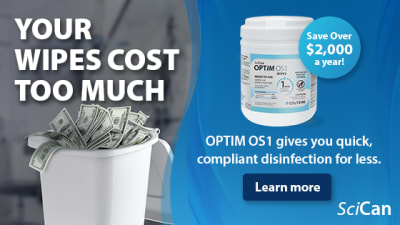
Your wipes cost too much
Zirconia
Not all commercially available -zirconia powders are the same. Differences between products in grain size and additives greatly control the material’s strength, long-term stability, and translucency.1 Furthermore, the varying processes by which dental zirconia powders are formed into milling blanks significantly influences the quality of the final product. Unidirectional axial pressing creates a milling blank shape that is very precise but lacks material consistency; therefore, it is not ideal for larger restorations.2 Another process, cold isostatic pressing (CIP) uses a liquid medium to apply pressure uniformly in all directions to zirconia powder enclosed in a mold to maintain its shape.3
The first generations of high-strength CIP zirconia milling materials resulted in monochromatic and densely opaque restorations that exhibited limited esthetics unless layered. However, during the past 5 years, newer iterations of zirconia materials have evolved into milling blocks with ever higher translucency and pre-shaded or multilayered blocks that greatly increase the esthetic outcome while reducing production processes. There are also fully sintered iterations created by hot isostatic pressing (HIP), which only require polishing after the milling process, making them suitable for chairside milling. Unfortunately, milling HIP zirconia is very slow and taxing on the milling unit and burs, increasing expense and the need for maintenance. Additionally, grinding dense sintered zirconia can introduce surface defects that may negatively impact the strength of the final restoration.4
Ceramics
Feldspathic Porcelain
The first CAD/CAM-produced inlay was made in 1985 using a feldspathic ceramic block.5 Feldspathic porcelain is currently available in millable form in VITABLOCS™ (VITA, vitanorthamerica.com) and CEREC™ Blocs (Dentsply Sirona, dentsplysirona.com). Vita™ Mark II blocks are fabricated using extrusion molding with feldspar porcelain particles embedded in a glass matrix, resulting in a reported flexural strength of 100 MPa to 160 MPa when glazed. The newer VITABLOCS, like TriLuxe™, Triluxe™ Forte, and RealLife™ blocks, come in color and translucency gradations that better match natural teeth for superb esthetics. CEREC Blocs are similar to VITABLOCS, but use a different shading system. The indications for millable feldspathic ceramic materials include veneers, inlays, onlays, and anterior crowns.
Leucite-Reinforced Glass-Ceramic
IPS Empress® CAD is a millable leucite-reinforced glass-ceramic first produced by Ivoclar Vivadent (ivoclarvivadent.com) in 2006. Leucite-reinforced glass-ceramics provide excellent blending results due to their natural translucency and chameleon-like effect. With more than 20 years of clinical data and an advertised flexural strength of 160 MPa, IPS Empress CAD is predictably indicated for veneers, inlays, onlays, and single-unit crowns.
As monolithic restorations gained popularity, IPS Empress CAD Multi blocks were developed to provide a seamless shade transition from the higher-chroma cervical area to a lifelike translucency at the incisal with optimal esthetics. Other leucite-reinforced glass milling blocks include the GC Initial LRF BLOCK (GC America Inc., gcamerica.com), which provides natural light transmission with a well-balanced translucency, fluorescence, and opalescent character, and the Paradigm C™ block by 3M ESPE (3m.com), which offers the same benefits and is indicated for inlays, onlays, crowns, and veneers.
Lithium Disilicate/Lithium Silicate
Lithium disilicate is available as a millable glass-ceramic produced by Ivoclar Vivadent under the product name IPS e.max® CAD. Known for its enhanced esthetics, IPS e.max CAD is milled in a pre-crystalized blue state that needs to be glazed and fired before delivery. This glass-ceramic displays moderate strength (360 MPa) with indications that include veneers, inlays, onlays, single-unit anterior and premolar crowns, and 3-unit bridges (up to the second premolar as the terminal abutment).
Millable lithium silicate blocks have offered restorative solutions with similar results. Dentsply Sirona’s Celtra® Duo is a fully crystalized block that provides well-balanced translucency and opalescence for crowns, inlays, onlays, and veneers. VITA Suprinity® and Glidewell’s Obsidian® millable blocks (Glidewell Laboratories, glidewelldental.com) are two lithium silicate ceramic blocks that can be milled in the laboratory or chairside using a variety of available mills. Suprinity claims to possess a fine-grain, homogeneous structure that provides excellent material quality and consistency as well as a high load capacity and long-term reliability with an approximate flexural strength of 420 MPa. Glidewell’s Obsidian lithium silicate exhibits an average flexural strength of 385 MPa and is indicated for full-contour crowns, 3-unit anterior bridges, veneers, inlays, and onlays.
Resin-Ceramic Hybrid
Resin-ceramic CAD/CAM millable materials, like VITA Enamic®, Lava™ Ultimate (3M ESPE), and Cerasmart™ (GC America Inc.) are the newest and most exciting millable innovations because they combine the desirable properties of ceramics and composites. The ceramic characteristics of these materials provide added strength and improved adhesive bonding, and the composite characteristics minimize wear on milling tools and allow for smoother margins, faster milling times, and easier finishing. The indications for these materials include veneers, inlays, onlays, crowns, and implant-supported crowns.
Composites
3M™ Paradigm™ MZ 100 by 3M ESPE is a traditional millable composite. It requires little post-processing beyond polishing, so it is considered a fast and easy alternative to ceramic blocks. This radiopaque material is available in six common shades, has a flexural strength of about 150 MPa, and is indicated for veneers, inlays, onlays, and crowns. Some of the advantages to milled composite are that the material is kind to milling tools as well as opposing dentition and that it is easier to add to after milling if needed.
Metals
The milling of metal is particularly appealing in dentistry because it eliminates the risk of miscasting. Two different types of metals are used for milling dental restorations: titanium and chrome cobalt. Both of these metals are biocompatible and corrosion-resistant, making them ideal for use in dentistry. Chrome cobalt lends itself to inexpensive milled crown-and-bridge frameworks onto which porcelain can be built, and titanium blanks with the appropriate machined implant interface are available to mill custom abutments. Titanium can also be anodized in the desired color to prevent metal show-through, even under soft tissue and zirconia restorations.
High-Performance Polymers/Resins (Plastics)
Polyether ether ketone (PEEK) has a long history of use in medicine in the fabrication of implant devices such as artificial cranial plates and spine implants. PEEK is a high-performance polymer with many desirable properties. It has a high strength-to-weight ratio and a bone-like modulus of elasticity. Therefore, PEEK frameworks are tough (170 MPa), but also lightweight and flexible. It has a zero corrosion rate and is hypoallergenic in nature, making it ideal for patients with metal allergies. It also displays a high resistance to wear and abrasion.
Pekkton (thermoplastic polyaryletherketone), distributed by anaxdent North America (anaxdentusa.com), offers a wide range of benefits, particularly for the making of implant-supported bars, abutments, and cement-retained prosthetics. The high-performance polymer has compression abilities and acts as a shock absorber.
PEEK and Pekkton are used in the digital dental CAD/CAM workflow to mill removable partial denture frameworks and fixed restorations, including crowns, 3-unit bridges, custom implant abutments, implant-supported superstructures, and telescopic copings.
High-performance polymers also offer great advantages in the removable partial denture space. Acetal (polyoxymethylene)—a product used heavily in manufacturing that has been adapted to dental use—is offered in millable puck form and used to provide a lightweight, metal-free, esthetic partial denture. Acetal is sold in the US as Duracetal® from Myerson Dental (myersontooth.com) and Zirlux Acetal® from Zahn Dental, a Henry Schein Laboratory Division (henryschein.com). A new entrant into the removable denture arena is Solvay Dental 360 (solvaydental360.com) with their Dentivera™ milling discs made from Ultaire™ AKP.
Polymethyl Methacrylate
Polymethyl methacrylate (PMMA) is available from many manufacturers in large pucks that can be milled to produce a variety of long-term provisionals, from single-unit crowns to full-arch bridges. These resins have flexural strengths comparable to feldspathic porcelain (ie, 130 MPa) and great color-stability for extended life. PMMA also provides an inexpensive method for producing “prototype restorations,” which patients can try-in to confirm marginal fit and esthetics prior to having the laboratory mill the definitive restoration in the final desired restorative material. Recently, there has been a great deal of excitement surrounding PMMA material as it has become the material of choice for digital denture solutions. Amann Girrbach, VITA, Ivoclar Vivadent, and Merz Dental (en.merzdental.de) all offer in-house millable digital denture solutions utilizing this material.
About the Authors
Alan Jurim, DDS
Private Practice
Woodbury, New York
General Manager
Jurim Dental Studio
Barbara Jurim, DDS
Private Practice
Woodbury, New York
Co-Founder
Jurim Dental Academy